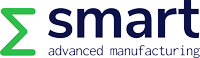
Gipuzkoa Science and Technology Park.
Paseo Mikeletegi, 59.
20009 San Sebastián. SPAIN
+34 943 309 009 – info@smarteureka.com
COORDINATOR
LTU
PARTNERS
Guaranteed
Winteria
VOLVO CONSTRUCTION EQUIPMENT
Smulders Group NV
LMI
JHS
HIAB
BWI
▪️ Project leaflet: download
Gipuzkoa Science and Technology Park.
Paseo Mikeletegi, 59.
20009 San Sebastián. SPAIN
+34 943 309 009 – info@smarteureka.com